Ten-year milestone for KNAPP team at Clarks
7th August 2015
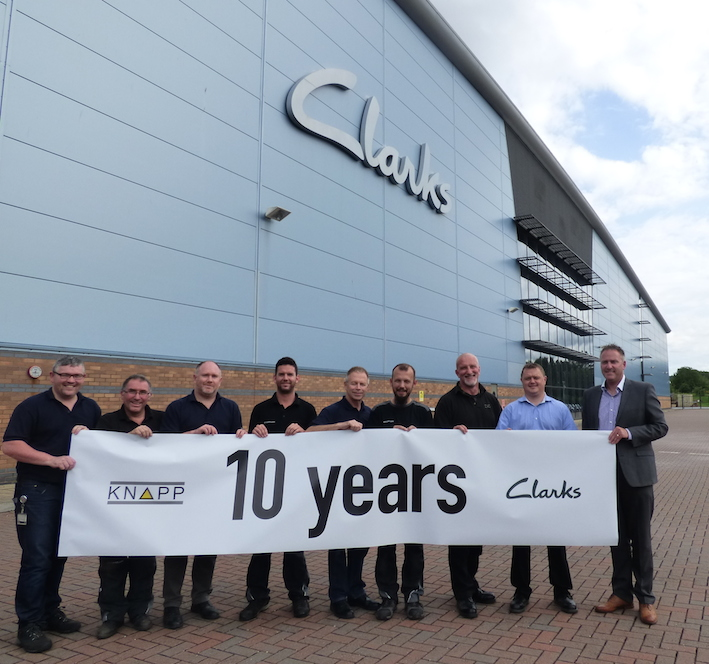
The resident team of KNAPP service engineers at the automated warehouse of Clarks, the global shoe supplier, recently celebrated ten years on site.
Present since the automated logistics solution at Clarks Westway distribution centre in Street, Somerset, went live in June 2005, the KNAPP team provides a comprehensive service of preventative maintenance and emergency repair to ensure maximum system availability. The team consists of 14 skilled engineers and is led by Kevin Ashman, KNAPP UK Ltds Site Manager at Clarks. This was the very first KNAPP resident team put in place in the UK, explained Kevin Ashman, so the structures and systems we devised here formed the blueprint for the subsequent resident teams, which now total eight in the UK.
The 10-year milestone was marked by a celebratory meal at a local restaurant for employees and directors of KNAPP and key members of Clarks logistics team, along with the presentation of engraved watches to the members of the service team by Craig Rollason, Managing Director of KNAPP UK Ltd, who emphasised that the team had acted as a key point of contact with Clarks. Having members of our team on site has undoubtedly helped us to understand Clarks evolving business needs, said Craig Rollason, especially the growth of its e-commerce sales and its international franchise operations. We helped Clarks to manage the move to multi-channel in 2008, allowing Westway to serve not only Clarks retail stores and wholesale clients but also individual consumers through its Home Delivery and Collect from Store services.
Craig Rollason (Managing Director, far right) and Nathan Billing (Regional Operations Manager East & South, second from right) joined Kevin Ashman (Site Manager, third from right) and some members of Clarks and the resident service team to celebrate KNAPPs 10 years on site at Clarks Westway DC
Capacity for six million pairs of shoes
Westway is the size of seven football pitches and has the capacity to hold six million pairs of shoes. With a core team of almost 300 employees, supplemented by additional temporary staff in peak periods, the facility operates 24 hours a day and seven days a week to ship shoes to 80 countries worldwide. Today Clarks has an extensive SKU range and a despatch peak during the back-to-school period. The automated systems include telescopic unloading conveyors at goods-in, an automated storage and retrieval system (ASRS), conveyor systems serving the picking areas on a mezzanine, a 600-chute sorter and shrink wrappers. The ASRS consists of 25 cranes operating in aisles 125m long and 12.4m tall. Unusually, incoming goods are not decanted into totes but rather the cardboard outers are handled directly by the cranes and stored double deep both sides; this avoids unnecessary handling of goods for volume orders, such as to wholesale customers.
Powerful payback
The success of the warehouse automation at Westway, concluded Craig Rollason, has undoubtedly been underpinned by the dedication of our resident service team. The cost efficiencies achieved here led to KNAPP being appointed as supplier of the automated handling systems for Clarks US operation at its 451,000 sq ft logistics facility in Hanover, Pennsylvania, in 2012. With another of KNAPP UKs clients set to celebrate the 10-year anniversary of its resident service team next year, we are delighted that we have been able to maintain excellent relationships with our clients over such long periods, and that the performance of our systems ably demonstrates the powerful payback offered by warehouse automation.